Light Laser Welding vs Traditional Methods: A Comprehensive Comparison
Release time:
2025-05-30
Light Laser Welding vs Traditional Methods: A Comprehensive Comparison Table of Contents 1. Introduction to Welding Technologies 2. Understanding Light Laser Welding 3. Traditional Welding Methods Explained 4. Comparing Light Laser Welding and Traditional Methods 5. Advantages of Light Laser Welding 6. Disadvantages of Laser Welding 7. Advantages of Traditional Welding
Light Laser Welding vs Traditional Methods: A Comprehensive Comparison
Table of Contents
- 1. Introduction to Welding Technologies
- 2. Understanding Light Laser Welding
- 3. Traditional Welding Methods Explained
- 4. Comparing Light Laser Welding and Traditional Methods
- 5. Advantages of Light Laser Welding
- 6. Disadvantages of Laser Welding
- 7. Advantages of Traditional Welding Methods
- 8. Disadvantages of Traditional Welding Methods
- 9. The Future of Welding Technologies
- 10. Conclusion
- 11. Frequently Asked Questions (FAQs)
1. Introduction to Welding Technologies
Welding plays a crucial role in various industries, from manufacturing to construction. In recent years, the industry has witnessed significant advancements, particularly with the introduction of **light laser welding**. This modern technique stands in contrast to traditional welding methods, which have been the backbone of metal joining processes for decades. Understanding the differences between these welding technologies is essential for industry professionals seeking the most efficient and effective solutions for their projects.
2. Understanding Light Laser Welding
Light laser welding, a process that utilizes concentrated laser beams to join materials, has emerged as a game-changer in the welding landscape. The laser's focused energy allows for precise and rapid heating, leading to effective fusion of metals.
This technology operates under various principles, including:
- **Continuous Wave Laser Welding:** Involves a steady beam of laser light, allowing for deep penetration and speed.
- **Pulsed Laser Welding:** Utilizes short bursts of laser energy, ideal for delicate materials or thin sections.
The versatility of light laser welding makes it suitable for diverse applications, including automotive manufacturing, electronic assembly, and aerospace engineering.
3. Traditional Welding Methods Explained
Traditional welding methods encompass several techniques such as:
- **MIG (Metal Inert Gas) Welding:** Uses a continuous wire feed and an inert gas shield to protect the weld pool from oxidation.
- **TIG (Tungsten Inert Gas) Welding:** Involves a non-consumable tungsten electrode and provides high-quality welds on thin materials.
- **Stick Welding (SMAW):** Utilizes a consumable electrode coated in flux to create a weld when an electric arc is struck.
These methods have served industries well for years, providing reliable and robust joints for various applications.
4. Comparing Light Laser Welding and Traditional Methods
When comparing light laser welding and traditional methods, several factors come into play:
- **Precision:** Light laser welding offers superior precision due to its focused energy, minimizing thermal distortion.
- **Speed:** Laser welding typically operates at faster speeds, reducing overall cycle time.
- **Heat Affected Zone (HAZ):** Laser welding results in a smaller HAZ, which is crucial for maintaining the material properties of sensitive metals.
5. Advantages of Light Laser Welding
Light laser welding boasts numerous advantages:
1. **High Precision:** The ability to focus the laser beam allows for intricate welds in tight spaces.
2. **Minimal Distortion:** Reduced heat input leads to less warping and distortion in the workpieces.
3. **Versatility:** Capable of welding various materials, including metals, plastics, and composites.
4. **Automation:** Easily integrated into automated manufacturing processes, enhancing productivity.
6. Disadvantages of Laser Welding
Despite its benefits, light laser welding has its drawbacks:
1. **Initial Equipment Cost:** The initial investment for laser welding equipment can be high.
2. **Material Limitations:** Some materials may not weld well with laser techniques.
3. **Skill Requirement:** Skilled operators are necessary to manage the technology effectively.
7. Advantages of Traditional Welding Methods
Traditional welding methods continue to hold their ground due to several benefits:
1. **Established Technology:** Widely used and trusted, with a vast knowledge base and experienced professionals.
2. **Cost-Effectiveness:** Lower initial costs compared to advanced laser systems.
3. **Material Compatibility:** Suitable for a broader range of materials and thicknesses.
8. Disadvantages of Traditional Welding Methods
However, traditional methods come with their own set of challenges:
1. **Heat-Affected Zones:** Larger HAZ can impact the mechanical properties of the welded materials.
2. **Speed Limitations:** Generally slower compared to laser welding, affecting production timelines.
3. **Skill Variability:** The quality of the welds can significantly depend on the welder's skill level.
9. The Future of Welding Technologies
As industries evolve, the future of welding technologies lies in the integration of advanced methods like light laser welding. The demand for precision, efficiency, and automation will drive further research and development.
Additionally, ongoing advancements in laser technology, such as fiber lasers and disk lasers, will enhance performance, making laser welding more accessible and applicable across various industries.
10. Conclusion
In summary, both light laser welding and traditional methods have their merits and limitations. **Light laser welding** stands out for its precision and speed, while traditional methods remain reliable and cost-effective. The choice between these technologies should be guided by project requirements, material types, and available resources. As the industry continues to innovate, embracing the right welding technology will be pivotal for achieving optimal results in metal joining applications.
11. Frequently Asked Questions (FAQs)
What is light laser welding?
Light laser welding is a modern welding technique that uses concentrated laser beams to join materials with high precision and speed.
How does laser welding compare to MIG welding?
Laser welding offers greater precision and a smaller heat-affected zone compared to MIG welding, making it ideal for sensitive materials.
Can laser welding be automated?
Yes, laser welding can be easily integrated into automated manufacturing processes, enhancing productivity and consistency.
What materials can be welded using laser welding?
Laser welding is versatile and can join various materials, including metals, plastics, and composites.
Is laser welding cost-effective?
While the initial equipment cost is higher, the efficiency and precision it offers can lead to cost savings in the long run, especially in high-volume production settings.
Key words:
All
- All
- Product Management
- News
- Introduction
- Enterprise outlets
- FAQ
- Enterprise Video
- Enterprise Atlas
Recommend News
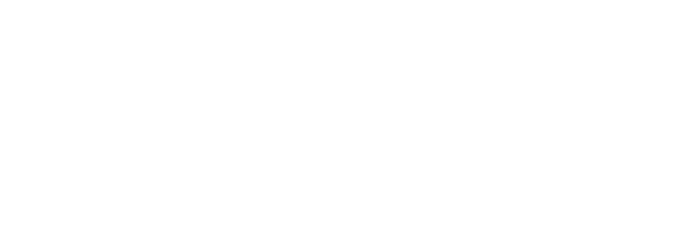




Contact Us
Phone: +86 (China) 152-5267-7152
WhatsApp: +86 (China) 152-5267-7152
E-mail:info@udibomfg.com
Address: Building 1002 Redstar International Technology Park, Mudu Town, Wuzhong District, Suzhou City, Jiangsu Province, China