Fiber Laser Welding Systems: Precision Solution for Automotive Manufacturing
Release time:
2025-06-16
Beam density up to 106W/cm², welding speed 50 - 200% faster than conventional methods. This ensures rapid production cycles for automotive components.
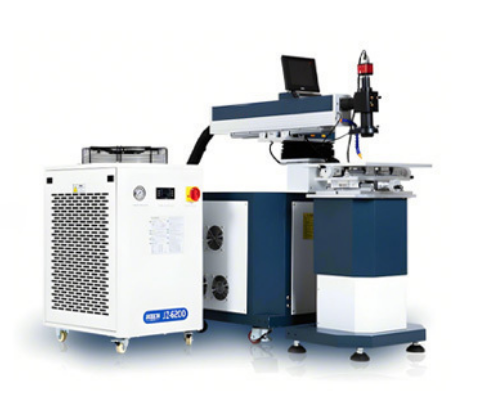
Technical Advantages
1. High Energy Density Processing
Beam density up to 106W/cm², welding speed 50 - 200% faster than conventional methods. This ensures rapid production cycles for automotive components.
2. Micro - Zone Thermal Control
Heat - affected zone (HAZ) limited to 0.1 - 0.5mm, reducing workpiece deformation by > 60%. Critical for maintaining precision in body panel fabrication.
3. Special Material Compatibility
Suitable for high - melting - point metals (Mo/Ti alloys) and high - reflectivity materials (Cu alloys). Enables welding of advanced automotive materials.
4. Non - Contact Processing
Focus lens lifespan > 10,000 hours, mold wear reduced to 1/5 of traditional processes. Minimizes maintenance costs for production lines.
5. Precision Process Control
Weld width tolerance ± 0.05mm, compliant with ASME Y14.5 standards. Ensures consistent quality in mass manufacturing.
6. Automation Integration
Supports robotic integration with real - time seam tracking, fully compatible with Industry 4.0 frameworks. Enhances production flexibility.
Automotive Application Cases
Lightweight Body Manufacturing
- Reliable joining of HSLA steel (1500MPa grade) and 6xxx aluminum alloys, reducing body weight by 15 - 25%. Enables fuel efficiency improvements.
- Battery tray welding porosity ≤ 0.8%, certified to UL 2580 safety standard. Meets strict EV safety requirements.
Powertrain Precision Welding
- Engine component welding deformation < 0.1mm/100mm, exceeding ISO 13919 requirements. Ensures smooth engine operation.
- Transmission gear weld fatigue life increased by 200%. Extends component service life.
High - Efficiency Production Lines
- Door assembly welding cycle time reduced to 12s/piece (1.5mm galvanized steel). Optimizes throughput for assembly lines.
- Overall Equipment Effectiveness (OEE) reaches 90%, maintenance costs down 35%. Improves manufacturing profitability.
Sustainable Manufacturing
- Wire - free process reduces consumables by 40%, certified to ISO 14046. Aligns with green manufacturing trends.
- Energy consumption per weld point reduced to 20% of conventional processes, cutting CO₂ by 2,800 tons/year per 100k bodies. Highlights environmental benefits.
Key words:
- All
- Product Management
- News
- Introduction
- Enterprise outlets
- FAQ
- Enterprise Video
- Enterprise Atlas
Recommend News
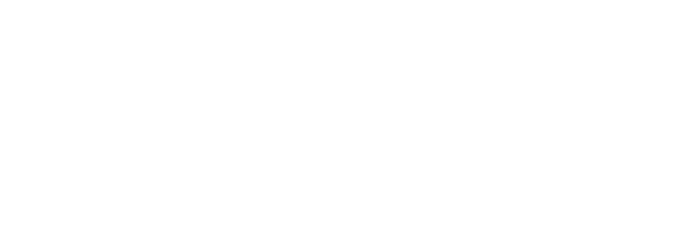




Contact Us
Phone: +86 (China) 152-5267-7152
WhatsApp: +86 (China) 152-5267-7152
E-mail:info@udibomfg.com
Address: Building 1002 Redstar International Technology Park, Mudu Town, Wuzhong District, Suzhou City, Jiangsu Province, China